Check out our most recent video that depicts our experience in El Salvador. Huge thanks to FUNTER, FUDEM, and all organizations that helped make our trip a success!
http://www.youtube.com/watch?v=UXheUzoCciw
Tuesday, November 30, 2010
Monday, October 11, 2010
August Newsletter
Friday, April 23, 2010
BYU Weekly | Prosthetics for Poor Countries
The idea of 2ftprosthetics was featured on BYU-TV today. Check it out!
Friday, April 9, 2010
1st Place - Social Venture Competition



Thursday, April 1, 2010
Saturday, March 6, 2010
Our first clinical trial
Our newest design
Here is our newest leg design, which we completed about two weeks ago. Instead of rivets, we used fishing wire to sew the PET (2 liter bottle) socket to the PVC support arms. We also incorporated a shoelace cinching system for loosening/tightening the socket.
Picture 1--The newest leg
Picture 2--Cutting out sole plate out of heated PVC
Picture 3--The socket sew in with fishing wire
Friday, March 5, 2010
Tuesday, February 16, 2010
How to vote for our project to help us go to Haiti and Africa
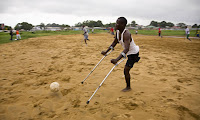
Vote for our idea on the Dell Social Innovation Competition website!
1) Google search 2ft prosthetics and click on the link for the Dell Social Venture Competition
2) Register (Just your email and a username are required)
3) Click on "Vote Now" at the top of the page
4) Click on the PROMOTE button for "Bringing hope to the lives of amputees one leg at a time" by 2ft Prosthetics
You can help! Thank you!
Monday, February 15, 2010
The sole of the foot
Facebook Cause
Hi all,
To help in the competitions I started a facebook "cause". It's called: "Help Amputees in Haiti and Uganda!" Feel free to join it and spread it!
To help in the competitions I started a facebook "cause". It's called: "Help Amputees in Haiti and Uganda!" Feel free to join it and spread it!
Thursday, January 28, 2010
Socket Design
I have tried to make a socket out of 4" dia. PVC sewer piping, and here are the results
We have also been testing out a heat-molding socket using a 2 liter bottle. However, I believe that we haven't found the ideal design yet. What other ideas do you guys have for an easy to make, inexpensive socket design?
Wednesday, January 20, 2010
Monday, January 18, 2010
Plaster of Paris casting test
We will test a few casting methods before we're done. This plaster of paris cast was easy to do, and made a good sculpture of my hand. There were heat warnings on the plaster of paris box, so the mold is of a glove and my fingers. Also, it is likely that the latex glove prevented the plaster from filling out the very fingertips. However, you can see where the fingernails go when you look at the positive mold!
Friday, January 8, 2010
Meeting With Roland Radack

Thursday, January 7, 2010
Prototype
Prep Meeting
We came together as a group today and talked about all of our accomplishments over the holiday break. It was neat to see all that was done in a short period of time.
Front Row: Peter, Carl. Back Row: Russell, Danny, Dave, Doug
Global Interest In 2ft Prosthetics!
Something neat I just found out: if you type in uganda prosthetics into a google search, a description of 2ft Prosthetics at dosomething.org will pop up as the 5th search return. I discovered this because Mindy Phung of Stanford University emailed us at the end of December expressing interest in becoming involved in our project. Isn't that exciting?! Let's keep spreading the word!
100,000 Cycles!!
We have reached 100,000 cycles of fatigue testing for the 4 piece foot!! The foot, which was made of PVC pipes of 3/4", 1", 1 1/4", and 1 1/2" diameter, easily endured a loading of 300-350 lbs without a problem.
Wednesday, January 6, 2010
The Four Piece
Tuesday, January 5, 2010
LDS Humanitarian Meeting Prep
Hey guys,
I spoke with Roland Radack today about our meeting with the Church Humanitarian group. He would like to meet with us this Friday at 2pm at his office in Salt Lake to discuss what we need to do to prepare for this meeting, and to also go over our business plan. Could any of you guys make it at this time, or would later (3 or 4) on Friday work for you better? Please let me know ASAP.
Dave
I spoke with Roland Radack today about our meeting with the Church Humanitarian group. He would like to meet with us this Friday at 2pm at his office in Salt Lake to discuss what we need to do to prepare for this meeting, and to also go over our business plan. Could any of you guys make it at this time, or would later (3 or 4) on Friday work for you better? Please let me know ASAP.
Dave
Subscribe to:
Posts (Atom)